Introduction
Dental medicine aims to restore health, function, and aesthetics, regardless of disease or injury to the stomatognathic system.1 Although total edentulism is decreasing due to improved oral disease control, the increasing average life expectancy and the consequent high number of elderly individuals lead to a higher risk of tooth loss.2
Removable dentures are a viable treatment option to replace missing teeth and soft tissue1-3 since they are easy to fabricate and repair and have good mechanical properties.4
Several resin polymers with different chemical compositions and types of polymerization reactions are used to produce removable dentures.5,6 Nevertheless, conventional production of heat-cured polymethylmethacrylate (PMMA) remains the most widely used and is considered the gold-standard fabrication protocol.3-6 Still, it has some disadvantages, such as the high number of clinical appointments needed,7 laboratory consuming time,4 polymerization shrinkage that could lead to maladaptation,8 allergenic potential due to the presence of residual methyl methacrylate (MMA) monomer,9-11 susceptibility to bacterial colonization,12 reduction of mechanical properties over time,13-15 and difficulty of performing an adequate duplication. 4 Thus, in an attempt to overcome these limitations, new materials and manufacturing techniques have been proposed.4,16,17
Digital denture manufacturing techniques reduce the cost and time of clinical and laboratory procedures,18 besides providing reproducibility by storing digital information.7,14
Three-dimensional (3D) printing is a simple and recently introduced additive digital denture manufacturing technique with low material waste.19,20 Materials developed for this technique are composed of less cytotoxic and more complex dimethacrylate-based monomers than MMA, such as urethane dimethacrylate (UDMA), bisphenol-A ethoxylate dimethacrylate (bis-EMA), triethylene glycol dimethacrylate (TEGDMA), and hydroxyethyl methacrylate (HEMA), and based on light-curing technology.9,20-24 Also, some authors have shown that light-curing printing techniques provide similar fit accuracy to heat-curing conventional methods.8,20,21,25 However, the additive technique with incremental layers can affect the polymeric network’s cohesive strength, leading to an increased probability of failures or fractures.21Therefore, studies evaluating the mechanical properties of 3D-printed resins for dentures are still necessary.
Since dentures must resist masticatory loads and plastic deformation induced by mechanical indentation or abrasion, the study of properties such as microhardness and flexural strength is important for clinical decisions on the materials and techniques to use.26-29 The aim of this in vitro study was to evaluate the mechanical properties of denture base resins manufactured by 3D printing and conventional techniques, according to the following null hypotheses: 1) there are no differences between the microhardness of the different resins studied; 2) there are no differences between the flexural strength of the different resins.
Material and methods
A power analysis was performed based on a pilot study to estimate the sample size of both tests (n=8) and provide statistical significance (α=0.05) at 80% power and an effect size of 0.25.13,30
Four denture base resins were selected: V-Print Dentbase (VOCO GmbH, Germany) and Denture 3D+ (NextDent BV, The Netherlands) as light-cured denture base resins suitable for 3D printing and Probase Hot (Ivoclar Vivadent AG, Liechtenstein) and Villacryl Rapid (Zhermack SpA, Italy) as heat-cured denture base resins for conventional production (Table 1). Eight parallelepiped-shaped (64x10x3.3 mm) specimens were prepared from each resin according to the respective manufacturer’s instructions and considering specific standards.31
Table 1 Characteristics of the material (composition, ratio, curing method, manufacturer, lot number, and expiration date)
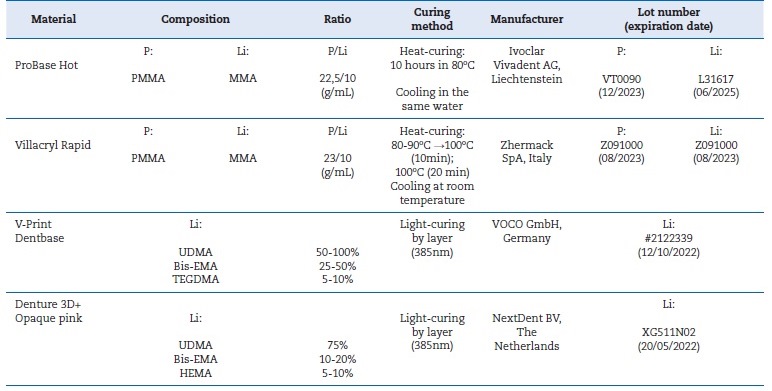
P - Powder; Li - Liquid; PMMA - poly(methyl methacrylate); MMA - methyl methacrylate; UDMA - urethane dimethacrylate; bis-EMA - bisfenol-A ethoxylate dimethacrylate; TEGMA - triethylene glycol dimethacrylate: HEMA - hydroxyethyl methacrylate
Printed specimens were designed with CAD 3D Sprint software (3D Systems, USA), and a standard tessellation language (STL) file was produced. Before printing, the Denture 3D+ liquid formulation was manually shaken for 5 minutes, followed by 1-hour agitation with the LC-3D Mixer machine (NextDent BV, 3D Systems, The Netherlands). The Denture 3D+ specimens were locally printed on a NextDent 5100 3D Printer device (NextDent BV, 3D Systems, The Netherlands), with a layer thickness of 50 μm. After printing, the specimens were cleaned with isopropanol, and a post-processing treatment was executed inside an LC-3DPrint Box (NextDent BV, 3D Systems, The Netherlands) for 30 minutes. V-Print Dentbase specimens were produced by the manufacturer (VOCO GmbH, Germany) from the STL file on a W2P Solflex 650 printing device (W2P Engineering GmbH, Austria), with a layer thickness of 50 μm. Then, specimens were cleaned with isopropanol (2+2 minutes), and the post-processing treatment was executed in the Otoflash G171 device (NK-Optik GmbH, Germany) during two cycles of 2000 flashes.
The heat-cured denture base acrylic resins Probase Hot and Villacryl Rapid were produced by a conventional flasking technique, according to the manufacturer’s instructions (Table 1). Probase Hot was produced using a long curing cycle (water until 80ºC, further maintenance for 10 hours, and cooling). Villacryl Rapid was produced using a short curing cycle (water until 80ºC, increase until 100ºC, further maintenance for 20 minutes, and cooling).
After processing, all specimens’ edges were grounded with a 600-grit silicon carbide paper (Carbimet Paper Discs, Buehler Ltd., USA) mounted in a rotational grinding and polishing machine (DAP-U, Struers, Denmark). Then, the specimens were soaked in distilled water and manually polished with polishing discs P1200 and P2500 (CarbiMet, Buehler, USA), 2 min each. Finally, each specimen was finished with 6-μm, 3-μm, and 1-μm monocrystalline diamond suspension (MetaDi, Buehler, USA) for 1 minute each. Polished surfaces were cleaned with an ethanol-soaked swab, and specimens were stored in distilled water at 37±2 ºC for 24 h in an oven (Ehret, Germany) before testing.32 Knoop microhardness was determined (Duramin, Struers DK 2750, Denmark) with 98.12 mN load for 30 s. The mean of six equidistant measurements made in each specimen was used as their corresponding microhardness value (KHN). Immediately after the microhardness test, flexural strength was evaluated using a 3-point bending device attached to a universal testing machine Instron Model 4502 (Instron, USA), with a 1-kN load cell at 5 mm/min crosshead speed and a span of 50mm. The width and thickness of each specimen were confirmed at three points with a digital micrometer (Digital Caliper, Mutitoyo, Japan).
Data were analyzed using IBM SPSS Statistics for Macintosh, version 27 (IBM Corp., USA). After assessing normality and homogeneity of variance (Shapiro-Wilk and Levene tests, p>0.05), microhardness data were analyzed with one-way ANOVA followed by Tukey post-hoc tests. Since normality (Shapiro-Wilk test, p=0.019) and homoscedasticity (Levene test, p=0.013) were not verified for flexural strength, data were analyzed with the non-parametric Kruskal-Wallis test. In all statistical tests, a significance level of 5% (α = 0.05) was considered.
Results
Microhardness mean values ranged between 11.6 KHN for V-Print Dentbase and 14.9 KHN for Villacryl Rapid (Table 2). ANOVA showed statistically significant (p<0.001) differences in microhardness between the resins tested (Figure 1). Both conventional heat-cured resins showed statistically significant (p<0.001) higher microhardness than the two 3D-printed light-cured resins. Comparing same-type resins, statistically significant higher microhardness values were found for Denture 3D+ (p=0.003) compared to V-Print Dentbase and for Villacryl
Rapid (p=0.01) compared to Probase Hot (Figure 1).
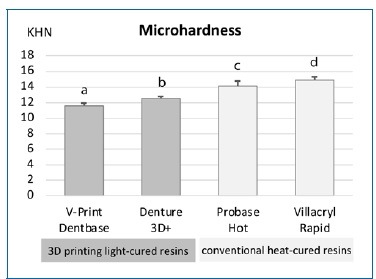
Figure 1 Microhardness (KHN) distribution of denture base acrylic resins’ groups (n=8). Bars with different letters were statistically different (p<0.05).
Regarding flexural strength, the highest mean value (123.8 MPa) was achieved with V-Print Dentbase, while Villacryl Rapid showed the lowest mean value (101.8 MPa) (Table 2). Despite these results, no statistically significant (p=0.527) differences were found in flexural strength between the four resins studied (Figure 2).
Table 2 Mean, standard deviation, median, interquartile range, and minimum and maximum values of microhardness (KHN) and flexural strength (MPa) per group of resins (n=8)
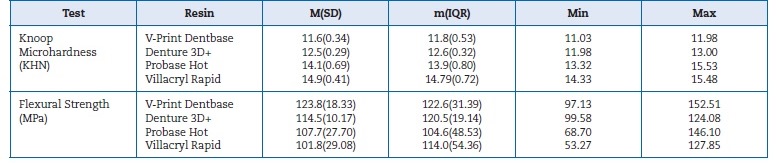
KHN - Knoop hardness number; MPa - Megapascal; M - mean; SD - standard deviation; m - median; IQR - interquartile range; Min - minimum value; Max - maximum value
Discussion
This study compared the microhardness and flexural strength of denture base resins produced by the digital additive and the conventional techniques. 3D-printed light-cured resins showed lower microhardness and similar flexural strength compared to heat-cured resins produced conventionally.
Higher microhardness in denture base materials is usually related to higher resistance to abrasion and surface wear.27 In the present study, printed resins based on light-curing dimethacrylate monomers showed lower microhardness than conventional heat-cured PMMA resins. Thus, this study’s first null hypothesis is rejected, which agrees with the literature.28 Different chemical compositions and the higher degree of cure associated with heat-cured resins may explain these results. Other studies concluded that 3D-printed acrylics had lower mechanical properties than most other denture base materials.7,26-28
Comparing the two 3D-printed resins, V-Print Dentbase showed lower microhardness than Denture 3D+. Despite having the same polymerization type, the different chemical compositions may lead to different mechanical properties.28
V-Print Dentbase has 20%-50% of bis-EMA in its composition against 10-20% in Denture 3D+ (Table 1), which can explain the reduction in microhardness due to bis-EMA usually increasing the viscosity of resins.23 Apart from the common monomers, the V-Print Dentbase resin comprises TEGMA, while Denture 3D+ resin contains HEMA. TEGMA monomer is added to reduce the viscosity promoted by bis-EMA but may negatively affect the mechanical properties due to promoting water absorption, increasing polymerization shrinkage, and leading to a greater release of residual monomer.23,24
The second null hypothesis was not rejected because the resins did not show significant differences in flexural strength. The light-cured printed materials V-Print Dentbase and Denture 3D+ obtained mean values similar to heat-cured conventional resins Probase Hot and Villacryl Rapid. These results do not agree with the literature, where printed resins have shown lower flexural strength than heat-cured conventional resins.26,28,33 Previous studies assumed that the bond between the layers of printed resins was weaker than the polymer network within each layer, which could be explained by the shrinkage stress and porosity that occur during light-curing.21,27,33,34Also, these polymers were made of different monomers with weaker bonds to the main matrix than MMA, which could result in a plasticizer effect on the core of the resin.23,24However, efforts have been made to improve the core properties of printed resins.
Factors like the width of each layer, the built orientation settings, and printing with recommended 3D printers can play an important role in optimizing the properties of printed resins to make them comparable to conventional ones.8,21,25
Specimens were stored throughout the study in distilled water at 37ºC. Like the humid environment of the oral cavity, water immersion exerts a plasticizing effect on resins, capable of interfering with their materials’ flexural strength.13 However, all groups showed flexural strength values above 65 MPa, the minimum value recommended for denture bases according to ISO standards for acrylic resins.13,31,35
One of this study’s limitations is having been performed in vitro under laboratory-controlled conditions, thus requiring a cautious extrapolation of the results concerning these materials’ behaviors in intraoral conditions. In the future, it would be relevant to further consider the biomechanical behavior of these resins submitted to physical, chemical, and mechanical aging to simulate the different biodegradation processes that denture materials are subjected to in the intraoral environment.
Another limitation is the variability of the flexural strength results, especially in conventional resins, which may indicate the need for a study with a larger sample.