Introduction
Portugal and the world have faced problems related to the generation of Municipal Solid Waste (MSW) and lack of alternatives for their final destination. To address different alternatives for final treatment, it can refer to recycling, composting, incineration, landfill and utilization of biogas production or other forms of energy. In Portugal, there are several MSW treatment units that have action plans to provide the compliance with the provisions of the Strategic Plan for Urban Solid Waste, PERSU 2020 (Ordinance No. 187-A / 2014)
According to this plan, the main goals to be achieved in 2020, based on 2013, enclose the increase of selective collection, reduction of biodegradable municipal waste deposition in landfill, increase the preparation for reuse and recycling flow and economic valuation of materials resulting from the MSW treatment (bioenergy, compost and refused derived fuels - RDF) engaging a circular economy strategy.
MSW is collected and then sent to a treatment unit - Mechanical and Biological Treatment (MBT) or a Mechanical Treatment (MT). After going through several recovery processes, there are always rejected flows with great potential, both at the physical and chemical level, as well as with a great recoverable energy potential, such as the RDF.
To achieve legal conformity, the RDF must have homogeneous characteristics with a significant caloric power and biogenic content, establishing an important factor for the sustainable management of wastes and resources, namely, avoiding the wastes landfilling and use them as an alternative fuel (Order No. 21295/2009).
RDF is the solid fuel prepared from non-hazardous waste, the use of which aims to recover energy in incineration or co-incineration units, in strict compliance with the legislation. The word "prepared" means processed, homogenized and improved to a quality that allows its exchange/commercialization between producers and users (NP 4486:2008). According with the same standard, the key parameters to classify a RDF are: lower heating value, chlorine and mercury content identifying the energetic potential, the technical and environmental features, respectively.
The ideal composition of RDF is the high content in plastics, excluding polyvinyl chloride (PVC), paper / cardboard, polymers, textiles, wood and other organic matter. Greater calorific value is in fact associated with paper / cardboard, plastics, wood and textile content and, since these materials have biodegradable compounds in their composition, it becomes an interesting alternative fuel to reduce CO2 emissions (Gendebien et. Al, 2003; Gallardo et al.,2014; Brás et. al., 2017).
In order to develop a RDF, the refuse from the main rejection line of the MBT needs to be prepared. For this, the waste is crushed into coarse and fine fractions, the separation of metallic contaminants and the separation heavy and light fractions. Fuels of different particle sizes and different technical specifications can be produced, maximizing the possibilities of incorporation into different production processes and, consequently, the quantities valued, depending on the needs of the market / customer.
Environmental advantages arise from the RDF utilization, namely the diversion from landfill of waste fraction’s that can potentially be valued and the reduction of greenhouse gas (GHG) emissions. The reduction of waste in landfills, removes much of the organic matter (between 40% to 60%), reducing biological activity, which translates into a decrease of about 95% of the CH4 that would be emitted without the MBT (IPCC, 2006).There are still obvious economic advantages to be considered, such as an increase in the landfill's useful life, which consequently allows to reduce costs associated with the landfill tax, which is 11€/ton in 2020 (APA, 2020) and its lower cost when compared to fossil fuels. It is worth notice the possibility of integration into a more advantageous tax regime for the production of electricity under a special regime (ERFO, 2010).
Keeping in mind these goals, this study focuses on the qualitative and quantitative characterization of the rejection line of a MBT from a Municipal Waste Management System (MWMS) and analysis of RDF produced from this line.
1. Methods
The samples were collected in the main rejection line (CT211) of the MBT unit of a MWMS. To collect a representative sample, the sampling was carried out during 5 consecutive days and stored in a 30m3 container. The physical characterization of each collected sample was done by manually sorting, separating plastic film, paper/cardboard, inert and discarded, and weighing each fraction. After the production of RDF, its characterization was done according with the solid recovered fuels European standards - number of samples (EN 15442:2011), type of waste (EN 15443:2011), particle size distribution (EN 15415-2:2011, proximate analysis (EN 15414-3:2011; EN 15402:2011; EN 15403:2011), elemental analysis (EN 15407:2011), heating value (EN 15400:2011), chlorine (EN 15408:2011), mercury and trace metals (EN 15411:2011) and major metals (EN 15410:2011).
2. Results
The MBT unit under study, that manages the MSW from several municipalities, is divided into three lines. One separates an organic fraction, under 60 mm for the organic digester, another recovers plastics, paper, metals or tetrapack containers for recycling and the third collects refuse from the other sorting units (CT211). This fraction may be potentially used for the RDF production This RDF must have homogeneous characteristics and high calorific potential with a significant biogenic content, constituting an important attribute for the sustainable management of wastes and resources, namely, through the diversion of wastes from the landfill and its use as an alternative fuel (Order No. 21295/2009).
2.1 Physical characterization of the rejected fraction
The CT211 line characterization showed that with an average belt speed of 23m/min, is produced about 10 ton/hour of rejected, which is equivalent to approximately 240 ton/day. From this line, representative of the MSW that are sent to landfill, 29% is paper/cardboard, 6% is plastic and 59% are textile, wood and other energetic materials useful for RDF production. The missing fraction is lost in the line and inerts (rocks and glass) - 5%. These results are similar to the presented in other studies, namely relatively to the plastic, paper and cardboard, and also textile or wood amount (Gendebien et al., 2003; Ranieri et al., 2017). It can be said that the selective collection strategies followed in different parts of Europe are having similar results once the fraction of these materials that are found in the undifferentiated MSW is relatively comparable.
2.2 RDF production and representative sampling
The RDF production process begins with the wastes transference from the container to a conveyor belt by a loader and are transported to the first shredder (Terminator type) for size reducing. After crushing, the flow passes through a magnetic separator, where all metallics are removed. The refuse follows on conveyor belts through a cyclone system and again through a blade crusher for final shredding, where the final RDF is achieved as a fluff.
Through a mass balance it was possible to verify that of the 6 tons of waste that were initial collected, only 780 kg of RDF were produced, an efficiency of 13%. This situation arises from the process specifications, suitable for a type of customer, which defines the meshes for crushing, the level of metallic separation through magnetic separators, the separation of heavier and lighter wastes by the cyclone. Considering the annual data of rejected production, it is possible to predict that, on average, 84972 tons of rejected are produced per year and, with a productivity of 13%, is possible to overcome an annual RDF production of 11046 tons, if the same technical specifications are maintained. Better production can be achieved with the optimization of the RDF preparation.
For definition of number and amount of samples for further characterization of RDF it was followed the methodology presented in the EN 15442:2011. The minimum sample size must be large enough to have enough particles to obtain a representative sample for the total assay. Before any sampling, it is important that the sampling objectives are clearly identified. This aspect is even more important, since the sampling itself can be done in the production phase, with collection on a conveyor belt, or in the storage phase, in a box or pile as described in EN 15442: 2011. The sample amount was estimated by equation 1 (EN 15442:2011).
Where mm is the mass of the minimum sample size (kg); d95 is the nominal top size of particles - a mass fraction of 95 % of the particles are smaller than d95 (mm); f is the shape factor (mm3/mm3); λ is the average particle density of RDF (kg/m3); g is the correction factor for distribution in the particle size; p is the fraction of the particles with a specific characteristic (kg/kg) and is equal to 0,1; and cv is the coefficient of variation, here set to 0,1. The determination of the nominal top size (d95), is based in the results shown in Figure 1, the granulometric characterization of the RDF produced.
According with Figure 1 it is noticed that 82% of the sample pass the 50 mm sieve, the higher sieve used, not being able to evaluate the d95. So it was considered, by approximation, that the diameter of 95% of the sample as diameter lower than 50 mm. Bearing in mind that the sample is quite homogeneous, it was also considered that the value of d95/d05=1. This parameter is needed to choose the correction factor for distribution in the particle size (g) that is 1 (EN 15442:2011) The shape factor, f, is calculated by equation 2.
Where V95 is the maximum volume of a fluff particle and was evaluated as V95=40x10x5 mm3. The attained f was 0.016. The density was accepted as 1000 kg/m3, p and cv of 0.1 (EN 15442:2011, 2011). With this data the mass amount for sampling should be 942g or 12L, (if apparently density is 77 g/L). Following the block method, a sample of this mass subdivided into 5 samples was taken for further analysis.
2.3 Proximate analysis
The proximate analysis was based in the evaluation of moisture, ashes, volatile matter and fixed carbon (Figure 2). In this graphic, some data from other authors are presented.
Moisture and ashes for RDF are 33.3% and 15.5% respectively. Looking for data presented by Zhao (2016) it is noticed a great difference probably due to the high heterogeneity of the sample. Gallardo and co-authors did not report the moisture because the results are presented in dry basis. The most different value was present by Brás et. al., (2017), with a very high moisture 53% probably because is related to the characteristics of raw materials for RDF production, and not effectively RDF. All the other data are similar.
According to some authors, RDF with moisture below 20% is desired for cement industries and can be valued as alternative fuel (Mokrzycki & Uliasz-Bocheńczyk, 2003). High moistures content as a negative impact in the lower heating value and, consequently in the combustion efficiency, in the gaseous emissions like carbon monoxide, sulphur dioxide and nitrogen dioxide. However, in this industrial process, the high temperatures, the oven area and length, as well the alkaline environment within, allowing the use of these fuels with economic and environmental advantages (Brás et. al., 2017).
The volatile matter achieved in the RDF was 86% (dry basis) with 0,87% of fixed carbon.
2.4 Chemical characterization of the RDF
The elemental analysis is very important to characterize the RDF once it relates the carbon and hydrogen content for further combustion processes. Moreover, it show the amount of nitrogen and sulphur that related the potential harmful gaseous releases, namely the emissions of sulphur
dioxide and carbon dioxide and also nitrogen oxides responsible for photochemical smog and greenhouse effect. Results of the RDF and from several authors are shown in Table 1.
Table 1 Elemental analysis values for RDF and values found in the bibliography
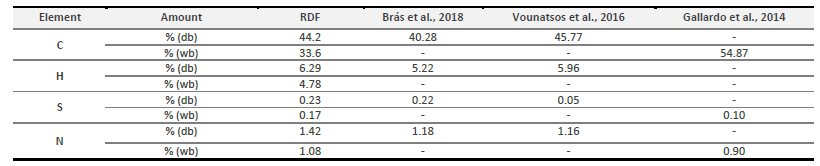
db - dry basis; wb - wet basis
Hydrogen, nitrogen and sulphur content are similar in the RDF prepared in this work and with other data reported in the bibliography. What concerns the carbon content only Gallardo et al. (2014) reports higher values, what is probably related with the reject fractions used for specific RDF production by these authors.
The determination of the major and trace elements content in the RDF is important for technical reasons both in the production and combustion phases, but again for the environmental impact. The determination of the major elements, such as Al, Ca, Fe, P, K and Na can be useful to predict the behavior of ash melting and scoring (McKendry, 2002). The trace elements like Cd, Cr, Cu, Pb, Mn, Ni and Zn, considered heavy metals that will end up being deposited in the soil, absorbed by plants and then ingested by animals, with high impact in global health. The results are shown in Table 2.
Table 2 Major and trace metals contents in RDF samples and data reported by several authors
Element | Unit (db) | RDF | Italian legislation (Genon et al., 2008) | Zhao et al. (2016) | Genon et al. (2008) | Gallardo et al. (2014) | Brás et al. (2019) | Ranieri et al. (2017) |
Cu | mg/kg | 23.2 | 50; 300 | 23 | 45-266 | 108.92 | 18.3 | 51.82 |
Zn | mg/kg | 8.7 | - | 18 | 225-340 | - | 547 | 107.04 |
Mn | mg/kg | 48.0 | 200; 400 | 7 | 28-210 | 136.27 | 41.8 | 36.88 |
Cr | mg/kg | 16.0 | 70; 100 | 2.6 | 11.3-140 | 135.49 | 16.7 | 9.922 |
Cd | mg/kg | 0.064 | 3; <7 | 0.05 | 0.18-2.6 | 9.8 | 0.62 | < 0.50 |
Pb | mg/kg | 23.9 | 100; 200 | 4.9 | 25-157 | 63.86 | 25 | 198.31 |
Ni | mg/kg | 2.4 | 30; 40 | 2.4 | 0.85-21 | 19.92 | 1.48 | 2.582 |
Al | % | 0.2126 | - | - | - | - | - | 0.0926 |
Fe | % | 0.1703 | - | - | - | - | 0.258 | 0.18724 |
K | % | 0.4815 | - | - | - | - | 0.388 | - |
Na | % | 0.4068 | - | - | - | - | 0.198 | - |
Ca | % | 2.4951 | - | - | - | - | 2.2 | - |
Db - dry basis
The most important fact that can be verified is that the metals content is lower than the Italian law reference (Genon et al., 2008) the legal data known by now, opening up good prospects for its use. Comparing with other materials, the achieved results are similar excepted when comparing with the results from Brás et al. (2019), for Zinc and Cadmium. These results are due to the fact that the sample is very heterogeneous and the waste samples analyzed may have materials with a high zinc content. The same trend happens for cadmium content, with values of 0.62 and 0.064, in Brás et al. (2019) and for RDF respectively, 10 times lower. Higher amounts of heavy metals were reported by Gallardo et al., (2014), showing that the preparation of the RDF, namely the separation of unwanted raw wastes is very important in the final RDF obtained.
2.5 RDF classification according with the Portuguese standard
According with the Portuguese standard, the RDF parameters that must be evaluated are the lower heating value (LHV), the chlorine and the mercury contents. The higher heating value (HHV) is the amount of energy released per mass unit over a complete combustion in a calorimeter. This is the energy released per mass unit, in the presence of oxygen, under conditions that allow water to be as vapour at 0,1 MPa (NP 4486:2008). According with EN 15400:2011 is possible to evaluate the LHV from the HHV and the elemental analysis of the samples, namely the hydrogen content. Experimental data showed the average HHV of 25.3 MJ/kg (dry basis). Considering the amount of hydrogen in the RDF (6.29%) the LHV achieved was about 24.0 MJ/kg. What concerns the heating value, the RDF should be classified as Class 2, according with NP 4486:2008 (20 ≤ LHV < 25 MJ/kg). Chlorine and mercury contents are shown in Table 3.
Table 3 Chlorine and mercury contents in the RDF and other bibliographic data
Element | Unit | RDF | Italian legislation (Genon et al., 2008) | Brás et al. (2019) | Vounatsos et al. (2016) | Ranieri et al. (2017) |
---|---|---|---|---|---|---|
Chlorine (Cl) | % (db) | 0.75 | 0.7; 0.9 | 0.44 | 0.43 | 0.05 |
Mercury (Hg) | mg/MJ (wb) | 0.004 | 0.1; 0.4 | 0.009 | 0.29 | 0.005 |
db - dry basis; wb - wet basis
The results show that RDF’s chlorine content respects the Italian legislation. Italian legislation present the maximum content for two kinds of RDFs, the poor and the best. Taking this reference, the RDF produced in this work show a good quality. According with NP 4886:2008, the RDF is a class 3 in respect with chlorine content once it has a concentration between 0.6 and 1% (db). The mercury concentration evaluated was very low, even when comparing with results from other authors. Relatively this parameter, this RDF may be classified as Class 1 because the concentration is below 0.04mg/MJ (wb) (NP 4486:2008). The European Commission guidelines are presented in Table 4, where is also overviewed the RDF main properties. Is possible to see that only the moisture is a negative parameter for this RDF, above 10%, the highest value acceptable for a good RDF, what can be overcome by a drying system in the RDF’s production plant.
Table 4 Comparation Values of European Commission with RDF
LHV (MJ/kg) | Ash (%) | Chlorine (%) | Moisture (%) | |
European Commission RDF (Gendebien et al., 2003) | 18 ; 21 | 10 ; 15 | 0,2 ; 1 | 3 ; 10 |
RDF | 24.1 | 15.5 | 0.75 | 33.3 |
For commercial proposes, there are some indications that, for a RDF with the granulometry characteristics and obtained LHV and chlorine content, a price value of 25.5€/ton of RDF is acceptable (Caracol, 2016). Attending to the amount of daily production of rejected fractions (240 ton/day), the productivity of the RDF manufacture (13%) and the amount of RDF with 20 mm or higher (50%), is expect an outcome of 795.6 €/day. Considering the additional reduction of the landfill tax (11 €/ton) it is achieved a gain of 1138.8€/day. It is worth notice that the RDF moisture is still higher than the acceptable for RDF users (20%) what implies that within the RDF manufacture system it is required its drying for which the energy produced in the anaerobic digestion system or other local heat form can be used. Along with this investment, that range according with the type of equipment and productivity desired, and operative cost, there are several other issues that have to be taken into account. According to other authors, operative costs can be estimated between 15 to 20€/ton, depending of the RDF’s quality (Caputo and Pelagagge, 2002). Therefore, is expected that other than environment benefits, economic profits may arise from the RDF’s production and valorization.
Conclusions
The CT211 line characterization showed that with an average belt speed of 23m/min, is produced about 10 ton/hour of rejected, which is equivalent to approximately 240 ton/day. From this line, 29% is paper/cardboard, 6% is plastic and 59% are textile, wood and other energetic materials useful for RDF production. The missing fraction is lost in the line and inerts (rocks and glass) It was possible to verify that of the 6 ton of waste that were conducted for RDF preparation, only 13% are effectively used, taking in consideration the specific RDF production line, suitable for a type of customer (specific grinding meshes, the separation of metallic materials and the separation of heavier and lighter wastes by the cyclone).
The RDF produced had, on average, a moisture content of approximately 33%, 15.5% of ash and the LHV of 24.1 MJ/kg with a chlorine content of 0.75%, and 0.004 mg/MJ mercury, within the guidelines for these materials proposed by the European Commission. The same was conclude for major and trace metals content. According with NP 4486:2008, it is possible to classify the RDF produced from three parameters, calorific value, chlorine content and mercury content of class 2 in relation to LHV, class 3 and 1 in relation to the content of Cl and Hg, respectively.
In a mechanical and biological treatment unit, such as the case study, it is possible to recycle the undifferentiated fraction of MSW avoiding the amount of waste deposition in landfill with a positive economic and environment income.