Introduction
CORP utilization is of certain interest for the corrosion inhibition of agricultural machinery stored in open areas and under sheds. In this way, it is possible to solve simultaneously three problems: obtaining edible oil, disposing of waste and preserving the oil during temporary storage. Previous studies have shown high CORP IE(%) in neutral environments without surface-active ions. On the contrary, aggressive media with Cl-ions sometimes stimulate steel electrochemical corrosion 1. Such effect takes place if the steel is covered by the mixture of low-EA CO refining products. Obviously, it is necessary to modify the protective compositions by means of various additives. In the present work, the effect of CORP modified by Zn powder, MGr and MCNT on St3 CS CR and kinetic parameters was estimated in neutral NaCl media. To date, numerous works have attempted to utilize plant products for mitigating steel corrosion in various media. Although plant extracts are sometimes used to form protective coatings on metals 2,3, they are more often introduced into corrosive environments as metal corrosion inhibitors 4,5.
Experimental
For the experiments, unrefined CO was used. CO treatment with softened water (10 wt.%), by vigorous stirring, for 3 h, at 50-60 ºC, led to the formation of an emulsion, which stratified upon standing during a day. Its lower layer was an aqueous dispersion containing P, mucus, scraps of cellular tissue, etc. The upper layer was treated by HO with concentrated H3PO4 (0.05 wt.% CO), for removing non-hydratable P forms. The resulting oil had an AN of 7.8 mg KOH (CO of AN = 7.8). Then, HO was neutralized with a NaOH solution (15 wt.%), by vigorous stirring, for 3 h, at 60-70 ºC, in order to remove free fatty acids.
After SF precipitation and separation, the oil was sequentially washed with water and a C6H8O7 solution (10 wt.%), by vigorous stirring, at 90-95 ºC, for extracting residues.
AN of the resulting oil was 3.5 mg KOH. Then, CO of AN = 3.5 was dried at 90-95 ºC, and intensively stirred, in order to remove the traces of moisture 6,7.
CORP (P, HO, CO of AN = 7.8, SF and CO of AN = 3.5) were used as coatings for inhibiting St3 CS atmospheric corrosion. The compositions were modified by adding 50 wt.% Zn powder or 50 wt.% Zn powder + 0.1 wt.% MGr or MCNT (Table 1).
Zn powder (99.9 %), with the fractional composition of μm/wt.% 2-5 ~ 96, 5...10-4 and 10...20-0.01, was used. MGr, with the fractional composition of μm/wt.% > 88-0.9, 80...70-7, 70...56-71, 56...40-15.7 and below 40-5.5, was employed. MCNT were produced by catalytic pyrolysis of a propane-butane mixture, at 600-650 ºC, on Ni/Mg 8. MCNT had the following initial parameters: outer diameter of 10-20 nm; content of amorphous carbon of 0.3-0.5 wt %; specific gravimetric surface area not smaller than 144 m2/g-1; average pore volume of 0.22 nm3; and average effective pore size of 7 nm. MCNT were activated at 107 ºC, in an aqueous solution of concentrated HNO3 and H2SO4, in a 1:3 volume ratio. MCNT disperse composition was investigated by DLS (PCS), using a Photocor-FC correlator (UK).
The corrosion tests were conducted on St3 CS with the composition (wt.%): С (0.2); Mn (0.5); Si (0.15); Р (0.04); S (0.05); Cr (0.30); Ni (0.20); Cu (0.20); and Fe (98.36). The samples with the size of 70 × 30 × 3 mm were used for corrosion testing by the gravimetric method. The CO coatings were deposited by immersion of the samples into the bath containing the composition shown in Table 1, at 20 ºC, for 15-20 min. Then, the samples were kept in a suspended state, for a day, at room T, in order to drain the excess composition and allow the formation of a protective film. The film thickness the was gravimetrically estimated, assuming that the coating was uniform. After the corrosion tests completion, the samples were cleaned from films and corrosion products, degreased, dried and weighed. The corrosion IE(%)was determined by the formula:
where K0 and Kc are CR of uncoated and coated CS, respectively. The duration of the experiment in 0.5 M NaCl was 336 h, at room T.
Stationary PSP measurements, with a E step of 20 mV, were carried out in a three-electrode cell made of Pyrex glass, with separated anode and cathode spaces, at room T, with natural aeration. E values were measured relative to a saturated Ag-AgCl RE, and converted to the standard H2 scale. The WE was St3 CS, with a horizontal working surface area of 0.5 cm2, and it was reinforced into a mandrel made of epoxy resin ED-5, with a polyethylene polyamine hardener. The WE was polished without pastes, degreased with acetone and dried with filter paper. The AE was smooth Pt. A protective film of the test composition, with a thickness equal to 20±5 µm, was formed on the electrode surface, after 15 min. The BGE was 0.5 M NaCl. IEa(%) (at anodic E of -0.20 V) and IEEcorr(%) (at Ecorr) were estimated from PSP measurements, according to formula (A).
Results and discussion
In a 0.5 M NaCl solution, corrosion tests on St3 CS covered by films of the low-EA CORP showed that their IE(%) did not exceed 45 %, and increased as shown in Table 2 and row 1:
Introduction of 50 wt.% Zn powder into the low-EA CORP resulted in an appreciable increase in their IE(%). Moreover, Zn evened out IE(%) of different CORP components. This was probably caused by Zn more dominant role in the inhibition of CS electrochemical corrosion than that of surfactants-CORP constituents adsorbed onto the metal surface (Table 2).
Table 2 Relationship between the nature of the protective films and their corrosion IE(%) in a 0.5 M NaCl solution.

The addition of MGr to Zn-filled low-EA CORP coatings further decreased Zn powder C, thus reducing equipment conservation costs, while the use of activated MCNT allowed assessing the effect of the filler dispersion on IE(%).
Corrosion tests on CS covered by low-EA CORP films filled with Zn showed that their IE(%) with MGr powder addition was practically absent (Table 2). Moreover, in some cases, there was even a slight reduction in the IE(%) of some CORP.
The effect of MCNT addition to low-EA CORP films filled with Zn, at C of 0.1 wt.%, on the corrosion tests of coated CS samples, is illustrated in Table 2.
MCNT dispersion composition was determined by PCS (Fig. 1).
Fig. 1 shows that this system has bimodal distribution. The first peak corresponds to particles with a size close to 320 nm. The second peak corresponds to particles with a cross-section of (103 nm. Large particles are nanoobjects conglomerates. They were MCNT stochastically rolled up into agglomerates.
MCNT addition to CORP containing Zn powder, in 50 wt.% C, did not increase the corrosion IE(%), and even led to its decrease. Thus, although the modification of coatings based on CORP by Zn powder was very effective, the introduction of MCNT particles of various natures and degrees of dispersion was impractical.
This conclusion was verified by PSP studies on the electrochemical corrosion kinetics of CS covered with the appropriate coatings (Figs. 2-5). βa, βc, Ecorr, icorr, IE(%)corr and IE(%)a, at Ea = -0,20 V, are shown in Tables 3-6.

Figure 2 PSP curves obtained on CS: 1- uncovered; covered with CORP films of 2 - HO; 3 - CO of AN = 7.8; 4 - P; 5 - SF; and 6 - CO of AN = 3.5.
Table 3 CORP coatings IE(%) and their effect on the kinetic parameters of CS in a 0.5 M NaCl solution.

CORP, excluding CO of AN = 3.5, shifted CS Ecorr to the anodic region, in the order:
The icorr of St3 CS covered by these films increased in the order:
βa polarization curves coefficient, measured on CS St3 covered by the films, increased in the order (Fig. 2):
The ia of St3 CS without and with the protective coatings and their IE(%)a, at the Ea of - 0.20 V, increased according rows (5) and (6), respectively:
The considered materials (except CO of AN = 3.5) suppressed CS St3 cathodic process, with the change in βc coefficient according to the order:
The cathodic polarization curves are characterized by a limit current (ilim), which increased in the order (8):
IE(%) at Ecorr was maximum for CO coating of AN = 3.5 and minimum for CO coating of AN = 7.8, which is consistent with the corrosion tests data in a 0.5 M NaCl solution (Tables 2 and 3).
Zn powder addition to protective coatings levels out row (2), and significantly increases CS Ecorr with CO of AN = 3.5+ Zn and SF + Zn coatings (Fig. 3), row (9):

Figure 3 PSP curves obtained on CS: 1- uncovered; covered with CORP films modified with 2- HO + Zn; 3- CO of AN = 7.8 + Zn; 4- P+ Zn; 5- SF + Zn; and 6- CO of AN = 3.5 + Zn.
The icorr values of CS coated with the films of original low-EA CORP (Table 3, row (3)), and their analogs modified by Zn powder (Table 4, row (10), are comparable, although their positions are different:
Table 4 IE(%) of low-EA CORP coatings modified with Zn powder, and their effect on CS kinetic parameters in a 0.5 M NaCl solution.

βa polarization curves coefficient of CS covered by CORP films filled with Zn increased by more of dozens mV than those of the corresponding original low-EA CORP (Table 4). The highest IEa(%) was provided by P + Zn and CO of AN = 7.8 + Zn coatings (row (11)):
The ia of CS coated by CORP filled with Zn and, therefore, the coatings IEa(%), at Ea = -0.20 V, varied according to rows (12) and (13), respectively:
Moreover, ia of CS coated by CORP filled with Zn powder was noticeably lower than that without it (Tables 3 and 4). Rows (5) and (12) also differ markedly from each other. Thus, in row (12), minimum ia and maximum IEa(%) (row (13), at E = -0.20 V, correspond to CS covered by SF + Zn and, in (5) and (6), to the HO coating.
The differentiation in IEa(%), which depends on CORP nature, was smoothed out with Zn powder addition, as in the corrosion tests with 0.5 M NaCl (Tables 2-3 ).
Zn powder addition to the coatings was accompanied by an increase in βс, while all coatings on the CS surface (row (14), Table 4), in contrast to row (7), suppressed cathodic O2 reduction:
Zn powder presence in the coatings differentiated their IEEcorr(%) (Table 4). CO of AN = 7.8 + Zn coating stimulated CS electrochemical corrosion, apparently due to the high content of free carboxylic acids (row (16)).
MGr particles in CORP coatings filled with Zn prevented CS Ecorr shift to the anodic region (row 17). This effect was most pronounced in the SF + Zn + MGr coating (Table 5 and Fig. 4), where Ecorr value is comparable to those in Table 4.
Table 5 IE(%) of low-EA CORP coatings modified with Zn powder and MGr, and their effect on CS kinetic parameters in a 0.5 M NaCl solution.

The icorr of CS covered by CORP, modified by Zn and MGr, was higher than that of the unprotected CS (Table 5), i.e., there was a stimulation of CS corrosion (IEEcorr(%) < 0).

Figure 4 PSP curves obtained on CS: 1 -uncovered; coated with: 2- HO + Zn + MGr; 3- CO of AN = 7 .8 + Zn + MGr; 4 - P + Zn + MGr; 5- SF + Zn + MGr; 6- CO of AN = 3.5 + Zn + MGr.
βa polarization curves coefficients decreased in the row (18), approaching to those of the unmodified CORP (Tables 3 and 5), thus reducing the effect of Zn powder addition (Tables 4 and 5):
MGr addition to CORP coatings filled with Zn increased sharply ia. IEa(%) of CO coatings filled with Zn + MGr was markedly lower than that of similar Zn compositions (Tables 4 and 5), with the exception of SF + Zn + MGr coating. IEa(%) decreased in row (19):
The coarse-grained MGr particles introduced into the Zn-filled coatings interchanged βc (HO + Zn + MGr) and βc (P + Zn + MGr) in the row (14), preserving the tendency for decrease in this value, in rows (14) and (20), and in the values shown by Tables 4 and 5:
The cathodic ilim took place on CS covered byCO of AN = 3.5 + Zn + MGr and CO of AN = 7.8 + Zn + MGr coatings, whereby,
MCNT addition to CORP coatings filled with Zn had a negative effect on IEEcorr(%). Thus, if IEEcorr(%) < 0 and IEa(%) < 0, icorr and ia values increasе. βa polarization curves coefficients changed insignificantly, but those of βc decreased sharply (Fig. 5 and Table 6).
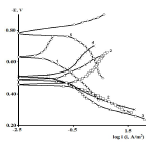
Figure 5 PSP curves obtained on CS: 1- uncovered; covered with: 2- HO + Zn + MCNT; 3- P + Zn + MCNT; 4- SF + Zn + MCNT; 5- CO of AN = 3.5 + Zn + MCNT.
Conclusions
Low-EA CORP IE(%), without and with modifying Zn powder, MGr and MCNT, has been studied on CS corrosion in a 0.5 M NaCl solution.
It has been shown that Zn powder (50 wt.%) addition to CORP made possible for it to achieve an IE(%) of 80-86 % in 0.5 M NaCl, which was probably due to its protective effect.
The effect of the protective coatings on CS corrosion kinetic parameters in 0.5 M NaCl was estimated.
MGr powders or MCNT addition to CORP modified by Zn powder had, in most cases, a negative effect on the coatings IE(%) and on CS corrosion kinetic parameters.
CORP coatings filled with Zn are promising as protective materials for temporary storage of machinery and spare parts under a shelter, in open areas and in unheated premises.
Acknowledgments
This work was supported by the Ministry of Science and Higher Education of the Russian Federation, in the framework of agreement no. 075-15-2021-709 (unique project identifier RF----2296.61321X0037). The results were obtained using the equipment of the Centre for Collective Use of Scientific Equipment of TSU, named after G. R. Derzhavin.
Authors’ contributions
V. I. Vigdorovich: conceptualized the study methodology; curated data; performed formal analyses; wrote the paper. E. D. Tanygina: performed the analyses; curated data. A. Yu Tanygin: collected data; made stationary PSP measurements. A. A. Uryadnikov: collected the corrosion tests data. L. E. Tsygankova: validated data; wrote the paper.
Abbreviations
AE: auxiliary electrode
AgCl: silver chloride
AN: acid number
BGE: background electrolyte
C6H8O7: citric acid
C: concentration
CORP: colza oil refining products
CR: corrosion rate
CS: carbon steel
DLS: dynamic light scattering
E: potential
Ea: anodic potential
EA: erucic acid
Ecorr: corrosion potential
H3PO4: phosphoric acid
HO: hydrated oil
i: current density
ia: anodic current density
ic: cathodic current density
icorr: corrosion current density
IE(%): inhibition efficiency
IEa(%): anodic inhibition efficiency
IEEcorr(%): inhibition efficiency at corrosion potential
ilim: limit current density
KHO: potassium hydroxide
MCNT: multiwalled carbon nanotubes
MGr: micrographite
MZn: microzinc
NaCl: sodium chloride
P: phosphatides
PCS: photon correlation spectroscopy
PSP: potentiostatic polarization
RE: reference electrode
SF: soap flakes
T: temperature
WE: working electrode